If you own or participate within a process you need a “CENTER OF TRUTH” a location where you can conduct research to see if a current “Disturbance to Flow” has previously been experienced and the corrective action taken ….
Doctors hate “Charting” as an attribute of their function but it is a highly necessary attribute so they can recall patient history.
Programmers hate “Documenting Software“… “it functions” but when enhancements or corrective action becomes necessary valuable time can be saved by not having to read and attempt to understand reams of code.
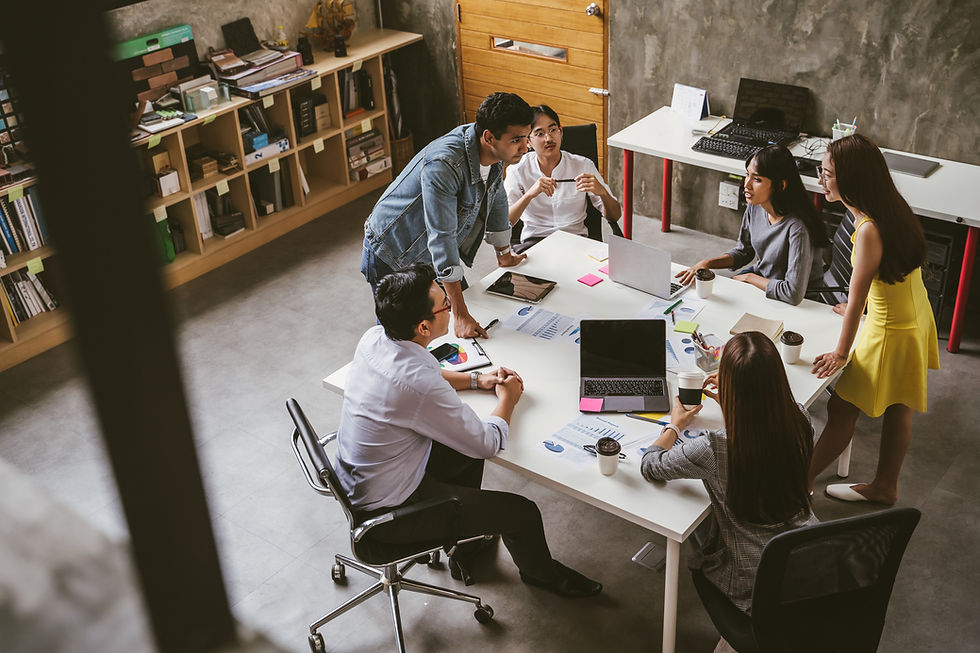
Documentation is a critical aspect of any process whether it is the history behind your automobile, your stay history with a hotel chain or decisions made with your lawyer while developing your “will” … all these ultimately become the “Centre of Truth”
Now R&D engineers like to work inside their labs letting their creative juices flow freely as a new breaking technology is developed and refined … but then …
THE HAND GRENADE operational excellence method transpires … as this R&D technology is thrust into operations to be replicated and produced at rate. Unfortunately the “Center of Truth” now becomes a virtue of Tribal Knowledge that only resides within your R&D Engineer. As I stated these R&D Engineers typically like the dark shadows of their lads so are not necessarily outgoing or accessible so our new technology falters and creates ongoing grief for the linear process experts now attempting to perfect the technology using a lottery mentality.
I consider that The Resident Love Goddess and I are seasoned Lean Practitioners. Our track record shows where we have doubled, tripled, and even quadrupled share prices allowed select sites to become benchmarks within multi-site corporations … so at the end of the day I feel that we know our stuff and know how to apply methodologies to create positive impact until recently …
We became introduced to a client that had become successful in spite of lacking formal
operational methodologies … they were doing well just based on the com-
mitment of dedicated employees and luck. A blank canvas for us … so off to
Work we went deploying known effective methodologies.
During the course of the next several months we introduced and implemented the following;
DAILY MANAGEMENT REPORT-OUTS where both the Employees and Management could reflect on previous 24 Hour Disturbances to Flow and mitigate upcoming concerns.
This definitely improved employee engagement but quality?
Next, we wanted to highlight Disturbances to Flow and not allow them to become “micro-stoppages” that would be ignored or just generally accepted … so we introduced Hourly Run Boards … yes hand-written and not electronic since we wanted to increase employee emotional attachment. Indeed this did surface more opportunities as we focused on the reduction of “Red” hours … but Quality?
In order to improve Process Up-time we then introduced TPM (Total Productive Management) which incorporated operator self checks of the process for early detection of potential problems but we expanded the reach to include other process related attributes … but Quality?
Of course the production schedule was erratic which we felt was impacting our KPI’s so we introduced 2 methodologies … 1) SMED so that our set-ups could be completed within minutes and no longer a concern as it related to schedule changes along with 2) a combined Raw Material and Finished Goods Kanban with an inherent Hyjunkia Box to allow for level loading and optimum schedule loading … this was overlaid on the existing ERP system for data collection and mining …. But Quality?
Our KPI’s continued to show huge opportunity to improve quality within process as our internal PPM was excessive although our defects were not escaping.
We placed a focus on Material Yield (one of my favorite metrics) … but the results were extremely positive as our yield numbers were consistently north of 95% which ultimately we found was helped by the fact that we could recycle scrap and defects back into the Raw Material Stream … so good use of material … but Quality?
We launched MORNING MARKET where quality and Process defects would be displayed for corrective action … in essence, make our quality concerns large and ugly begging for corrective action. But asking for action without a methodology just becomes a wish … the result was to launch aggressive A3 Training. We formed A3 Problem Solving Teams and allocated Team Time to work on A3. Our training had encompassed a formal problem-solving methodology suite of tools since traditional A3 methodology is just a reporting mechanism. We moved the needle slightly … but Quality?
It became extremely frustrating as our Quality KPI failed to significantly improve our Quality KPI and the resulting analysis of our Pareto Chart analysis showed that the primary Quality culprit was a recently introduced new product. This product had by-passed the formal route of New Product/Process introduction … so no CENTER OF TRUTH existed.
Full Stop !!!! Lean Methodologies implemented could not deliver their full potential until a CENTER OF TRUTH could be established.
So now we will back-up a bit and put the new product through an accelerated but reflective New Product Introduction flow … we know that we cannot overlook each important attribute like;
•Capturing the Voice of the Customer
•SIPOC
•Detailed Process Map
•Cause & Effect Matrix
•The very important and well thought FMEA
•Control Plan
So if you have successfully implemented your Daily Lean Methodologies to identify and resolve opportunities but it is not delivering the epitome result …. Back up further and re-build your foundation. Of course always use your “Problem Follow” sheet as you create your CENTER OF TRUTH
Comments