Every Process has a changeover to minimize or eliminate.
- Richard Kunst
- Sep 26, 2021
- 4 min read
There are two basic paths to achieving a quick changeover. I call them, loosely, organizational and mechanical. Either of them, individually, will achieve some good results. Together, they will achieve superior results.
I use the term "organizational" to refer to those aspects of changeover reduction which rely on improved procedures, processes, training, product design, organizational and managerial changes and the like. "Mechanical" refers to improvements to equipment such as eliminating or externalizing changeover steps, making all set-up adjustments measurable, replacement of older machines with newer, more changeover friendly, machines and tool elimination.
As with so many things, there may not always be a clear bright line between the two. I distinguish between them mainly because I believe that improving changeover can seem a pretty daunting task and breaking it down into smaller chunks can make it more manageable.
So let's take a brief look at a few of the steps along the organizational path:
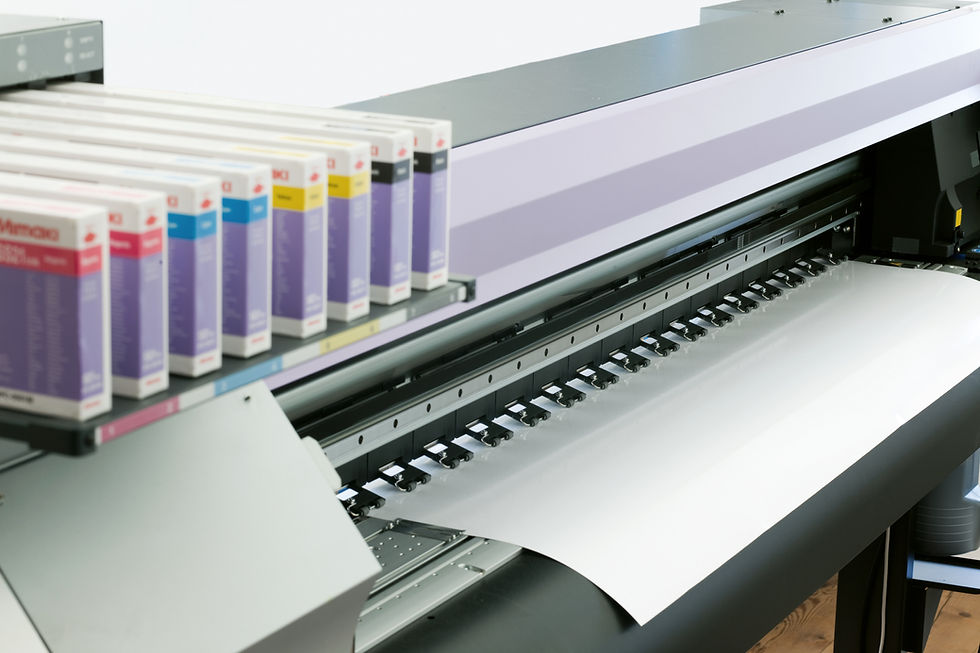
BUY-IN
If the people on the floor, the ones actually performing the changeover, do not buy into the idea of improvement, it is unlikely that much will occur. In the event that improvements do occur, it is even more unlikely that they will be held. The very first step in a successful changeover improvement program must be getting buy-in by the people involved. Absent that buy-in, they will do what they are told and little more. We can't succeed unless we can tap into the wealth of knowledge that they carry around with them.
One of the reasons we don't get buy-in is because they may not see what good the program does for them. We, in management, will tell them all the wondrous things that reducing changeover will do for the company
What we really need to do is look at each of them and imagine that on their foreheads they have tattooed WIIFM? In big red letters. WIIFM stands for "What's in it for me?" and is a question we must be sure to answer. Some of the positive things that are in it for them are easier work since it will be better organized and simplified, better job security as the company will be more profitable and opportunities to learn new skills and surmount new challenges.
There are also some negative issues that may be involved. Some may look at the project and think that what is "in it" for them is the loss of a job since not as many people will be required if changeover times go down and loss of status if work is simplified so anyone can do it. It is absolutely critical that both the positive and negative aspects be addressed to achieve buy-in
Management support
Essential to any changeover program is the support of company top management. If the boss is not behind the program, how can we expect anyone else to be? This support needs to be expressed in various ways. Statements of support and recognition are required, of course, but as they say "Talk is cheap". There also needs to be tangible support in the form of giving the team time to work on the changeover, training courses and materials, books and periodicals, and perhaps the opportunity to network with their peers in other areas of the company or even in other companies.
Documentation
I doubt that anyone will deny that work goes more efficiently "doing things right" as well as more effectively, "doing the right thing" (Tipping my hat to Peter Drucker) when the people doing it know what they are supposed to be doing. So why do I find so many companies that do not have any kind of written documentation for performing a changeover? They leave it to the mechanics and operators to muddle through, based on experience and, in some cases, luck. Then they can't understand why A) it takes so long and B) why the process is so uneven. One of the early steps must be to figure out what is being done and/or needs to be done and then documenting it in a "Standard Operating Procedure" or SOP (Some of you in other countries may have different names and I am always interested in learning!). Since you will be changing the changeover process anyway, should you write the SOP now? In my opinion, yes. If you do not know where you are starting from, you may not be able to get where you want to go.
Measurement
When I took business finance in grad school the mantra drilled into us was "If you can't measure it, you can't control it". This applies to changeover as well, though I have learned to add "If you don't measure it, you won't control it". How long does changeover take? Remember that when measuring changeover it is critical to include not just the cleanup and set-up but the start-up time. (Start-up is the time after the line is restarted but before it has settled down and is running at normal efficiency) If the start-up is not measured, it is far too easy to reduce the set-up time (by being quick and sloppy) at the expense of additional start-up time.
A goal or target needs to be set for changeover times. If there is no measurement, it is impossible to know if that goal is met. If management doesn't know if the goal is being met, it is impossible to insist that it be met. Measuring change over time is tough and takes some thinking (When does start-up finish?) But it can and must be done.
Comments