How to Solve 5 Problems in Operations
- Richard Kunst
- Aug 6, 2023
- 5 min read
Automation and robots are all the rage in operational management these days. In a 2022 survey, 60% and 45% of operations managers planned to invest more in equipment (new or upgrades) and information technology respectively. A separate survey found 96% of respondents expected the value proposition of automation to increase over the next 36 months.
Yet, employees remain a central pillar of operations. If your human resource management is in shambles, it’s going to be harder to make your operation a consistently efficient facility. Preempting employee problems is the first step to getting worker management right.
Here are some practical tips on how to overcome the most common employee management problems in operations.

1. Poor Scheduling
There’s a lot to gain from having your processes running like clockwork, and that greatly depends on the quality of your scheduling. Poor scheduling leads to missed shipments, delayed orders, unhappy customers and unproductive employees.
It seems like we always end up spending time with the scheduling team, in spite of leaders telling that their problems exist elsewhere.
Schedulers seem to want to schedule towards an infinite horizon but the reality is that your employees only want to know 2 things ... 1) What do you want me to do now and by when and 2) What do you want me to work on next?
As a leader it is very easy to get sucked into the weeds of scheduling ... STOP !! I use my BBB Report to insure our schedule is in balance. I monitor our Billings, Bookings and Backlog on a daily basis. As long as my Billings and Bookings stay in balance and the numbers meet my budget/plan I feel slightly relaxed and when my Billings divided into my backlog meet our delivery times I am elated. But, I do spend time insuring that our backlog is "Workable", because my people are constantly telling me "give me the parts and i can build it"
2. High Turnover Rates
A high turnover is disruptive to operations. Twenty-seven percent of businesses believe high turnover caused them to miss delivery timelines and production deadlines. Think about the learning curve all new staff must go through before they eventually take a firm hold of your processes. It comes with costly delays and mistakes. Additionally, there’s all the in-house and external training you invest in for each worker. This takes time and money.
Reduce worker turnover by offering good working conditions – introduce flexible working hours so employees feel like they can still accomplish their personal, family, educational and recreational goals without necessarily compromising their job security. Accommodate employee needs as much as possible (like having a creche at the workplace).
People want to feel that they belong and are appreciated and being heard ... so figure out how to put in place some communication channels to allow you to get unfiltered information.
3. Safety Hazards
Spills, slips, falls from height, falling objects and moving equipment are an ever-present danger. They jeopardize the safety of your employees and pose a risk to your operations. Fatality is the most severe consequence of operational hazards. It is not the only thing you should be worried about, though.
When employees are injured or fall ill, they have to take time off work, something that doesn’t reflect well on your operations. Add to that the impact of workers’ compensation claims.
Make safety a priority in your work environment. Provide enough space for employee movement and equipment maneuverability. Invest in forklifts to minimize the need for staff to reach for or place items at height.
I am now also cognizant to a hidden Safety Hazard that being many of your employees are getting distracted at work thinking about how to care for their elders and children, how to schedule appointments with the appropriate specialists. My innovative solution was offering a concierge service to our employees where the concierge would take the extended employee (family) to their scheduled appointments and allowing our critical resource to remain at work.
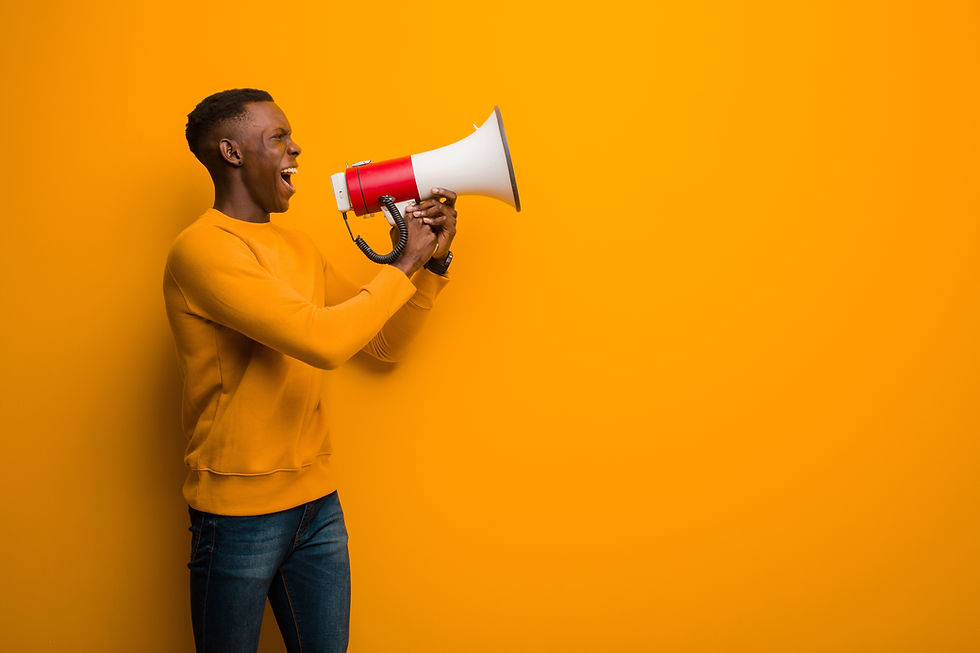
4. Lack of Communication
At any given point, do your employees know what they should be doing, where they should be and who they should be working with? A lack of communication is a recipe for operation dysfunction. Miss-picks, incorrect routing and scheduling conflicts represent just a snippet of what could go wrong. Executives and Operational Leaders cite a lack of communication and collaboration as the primary cause of workplace failure.
I can guarantee that even those organizations who go out of their way to over communicate the largest employee complaint will still be that a lack of effective communications exists. I have minimized this concern by implementing "Daily Management" that allows me to communicate with every employee every day and i only focus on what i need today and what do they need from me to make it happen and of course we celebrate yesterday's accomplishment. Simple, easy 3 minute stand-up meetings within my natural work groups.
Streamline communication and automate information dissemination wherever possible. Have employees automatically receive alerts about events relevant to them. Ensure everyone is kept up to date with the latest announcements and procedures. Pin critical updates to your Daily Report-Out board, online and onsite. Use read receipts to be certain key staff have seen important notices.
5. High Labor Costs
Labor constitutes as much as 50-70% of a your operations budget. It doesn’t help that every organization would want to hire the best-qualified people, and these tend to be the most expensive. When labor costs are higher than they need to be, they make it harder to run the business profitably.
Explore opportunities to reduce staff. You could cut your worker headcount, give a raise to those that remain (as motivation) and still enjoy significant savings on your overall labor costs. Continuously upskill your existing staff to curb the need for expensive outside experts. Simultaneously, identify processes that could benefit from partial or full automation.
As a reminder look at how many transportation companies you see as you drive around. Just remember they pay the same for equipment, they can only drive at the speed limit, and typically the traditional trucks have the same capacity so what is the differenator? Trucking companies with newer, shinier equipment will retain employees longer at competitive labor rates and they typically have a great driver lounge back at base.
Conclusion
Most organizations do not enjoy the luxury of infinite financial resources. There is only so much you can do to keep employees happy and loyal to your team. It’s all about striking the right balance between employee management and business profitability. The good news is it can be done.
BTW, this is not a new problem. These problems have been around forever, just under a different scenario in the 40's, 50's, 60's, 70's, 2020 and still today.
It can be mitigated, Evaluate your operations regarding the five key problems in employee management and identify the specific areas you can do better in. Schedule regular review of employee-related processes (at least annually) to ensure your business is always running at its best. You can also contact us for additional tips and tricks that have worked for us in the past.
There are actually several companies that are not struggling with these issues but that does not mean they ignore them, they constantly manage them front and center.
Comments