Six Sigma Methodology: How to Implement it in Your Business
- Richard Kunst
- Feb 23, 2024
- 14 min read
Whether your business is new or well-established, adopting Six Sigma can lead to improved performance, reduced costs, and more satisfied customers.
This guide simplifies the Six Sigma methodology and shows how it works well with Lean Six Sigma. You'll learn about the DMAIC process and see real examples of Six Sigma in action.
You'll also discover the Six Sigma Belts, the experts who make this all happen, and what it takes to become one of these skilled professionals. Next, you'll learn to distinguish between Six Sigma and Lean Six Sigma, helping you decide which fits your organization best.
Let's dive into it.
What Is Six Sigma? The Six Sigma Methodologies
Six Sigma is a disciplined, data-driven business approach and methodology for eliminating defects in any process – from manufacturing to transactional and from product to service.
Developed by Mikel Harry and Bill Smith in the 1980s at Motorola, the Six Sigma methods aim to improve the quality of process outputs by identifying and removing the causes of defects (errors) and minimizing variability in manufacturing and business processes.

Core Principles of Six Sigma
Six Sigma focuses on four core principles:
Focus on Customer Requirements: Six Sigma emphasizes understanding and meeting customer needs and specifications.
Use of Data and Statistical Analysis: Decisions are made based on data and statistical methods rather than assumptions or guesswork.
Process Improvement: Six Sigma seeks to improve the quality of process outputs by identifying and removing the causes of defects and minimizing variability.
Active Involvement of Employees: It involves employees at all levels, fostering a culture of continuous improvement.
By focusing on quality improvement and process optimization, Six Sigma principles have become a symbol of manufacturing and business excellence, with many organizations adopting its practices to enhance their competitiveness and performance.
How Does Six Sigma Reach Its Goals?
The Six Sigma methodology reaches its goals by incorporating various tools, including process mapping and a blend of statistical data analysis, along with tested qualitative and quantitative methods.
Six Sigma incorporates the following tools:
Brainstorming: Brainstorming is essential in problem-solving, often employed in the DMAIC methodology's "improve" phase. It's the starting point, where a group, led by a Black Belt or Green Belt, shares and develops creative solutions.
Root Cause Analysis/The 5 Whys: Root Cause Analysis, particularly the 5 Whys technique, delves into the primary cause of issues during the "analyze" phase of DMAIC. By repeatedly asking "why," it uncovers the underlying problem, adjusting the number of questions to achieve clarity.
Voice of the Customer: In the DMAIC's "define" phase, Voice of the Customer captures customer feedback to enhance products and services. It uses direct and indirect methods to understand and respond to evolving customer needs.
The 5S System: The 5S System, rooted in Japanese principles, aims to eliminate waste and inefficiency. Its steps, Seiri, Seiton, Seiso, Seiketsu, and Shitsuke, focus on organizing and maintaining a productive work environment.
Kaizen: Kaizen advocates for continuous enhancement, especially in manufacturing. It's a process of constant monitoring and refining to reduce waste and implement changes promptly.
Benchmarking: Benchmarking involves setting a standard for comparison. It's about measuring your practices against others, either within the same industry or against market leaders, to understand your position and improve.
Poka-yoke: Poka-yoke focuses on preventing errors before they occur. It encourages employees to identify and correct potential mistakes early in the manufacturing process.
Value Stream Mapping: Value Stream Mapping analyzes the current flow of materials and information to design more efficient systems. It aims to identify and eliminate waste, streamlining the process for better productivity.
What is Lean Six Sigma?
Lean Six Sigma is a strategy that combines two powerful methods: Lean Manufacturing and Six Sigma, to boost both business and operational efficiency.
It's a toolkit designed to enhance the quality of what businesses create by tackling flaws and reducing inconsistency in manufacturing and business activities.
Here's a closer look at how these two parts work hand in hand:
1. Lean Manufacturing
Lean Manufacturing, born from the Toyota Production System, aims to eliminate waste and enhance workflow. This part is all about making production smoother, shortening the time things take, and getting rid of what's not needed.
The aim here is to give customers more value using fewer resources.
2. Six Sigma
Six Sigma is a set of techniques and tools for process improvement.
Motorola introduced it in 1986, focusing on identifying and removing the sources of errors and minimizing unpredictability for customer satisfaction and business success.
Six Sigma uses various proven and statistical methods and relies on a team of in-house experts, known as "Black Belts" and "Green Belts," who are well-versed in the Sigma method.
When you blend Lean Manufacturing and Six Sigma, you get Lean Six Sigma — a strong structure for enhancing both the speed and quality of processes, leading to improved performance and reduced costs. Various industries embrace Lean Six Sigma to uplift the quality of their products and services, reduce waste, enhance efficiency, and boost customer satisfaction.
The combination of Lean's focus on speed and efficiency with Six Sigma's dedication to quality and precision makes Lean Six Sigma a formidable force for ongoing enhancement and organizational change.
Lean Six Sigma is more than a method; it's a commitment to continuous improvement using the Six Sigma methodology. For anyone looking to make their business processes better, Lean Six Sigma implementation offers a clear path forward.
It's not just about fixing what's broken; it's about setting a new standard for excellence.
Key Differences Between Six Sigma and Lean Six Sigma Methodology
Understanding the differences between Six Sigma concepts and Lean Six Sigma methodology can help you decide which one might be more suitable for your specific Six Sigma projects or organizational needs.
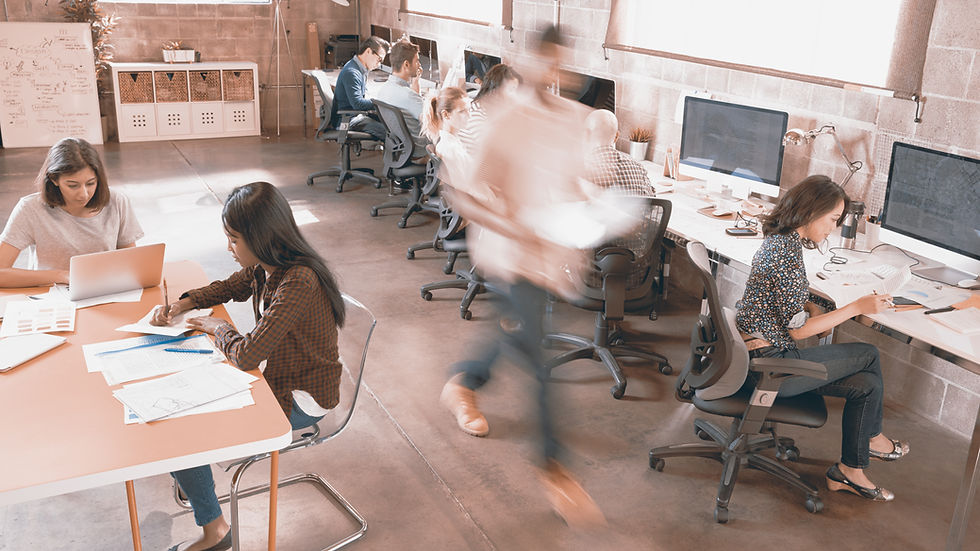
Both methodologies have their strengths, and often, they're used together to enhance both quality and efficiency in processes.
Here are some of the key differences you need to know:
Focus: Six Sigma primarily concentrates on reducing defects and improving quality by eliminating variability in processes. Lean Six Sigma, on the other hand, combines this focus with the Lean method's aim to remove waste and increase efficiency.
Approach: The Six Sigma process uses a structured, data-driven approach to solve quality issues and reduce defects, often using DMAIC (Define, Measure, Analyze, Improve, Control). Lean Six Sigma incorporates Lean's tools and principles to streamline operations and improve flow in addition to DMAIC.
Speed and Efficiency: While Six Sigma focuses on improving quality by understanding and reducing variation, Lean Six Sigma emphasizes speed and process efficiency, aiming to make processes faster and more cost-effective.
Tools Used: Six Sigma utilizes statistical and sigma tools to analyze and improve processes. Lean Six Sigma uses these tools plus Lean techniques like 5S, value stream mapping, and Kanban to enhance process speed and reduce waste.
End Goal: The end goal of Six Sigma is to achieve near-perfection in quality with fewer defects. Lean Six Sigma aims not only for high quality but also for swift and lean operations with minimal waste.
Implementation: Implementing Six Sigma typically involves more in-depth statistical analysis and may take longer to see results. Lean Six Sigma often yields quicker improvements by eliminating obvious waste in the process.
Flexibility and Scope: Six Sigma is often more rigid with a defined set of steps and statistical requirements. Lean Six Sigma is generally more flexible, adapting to different environments with a broader scope of tools and techniques.
Training and Certification: While both methodologies offer belt-based certification levels, Lean Six Sigma belts are trained in Lean principles in addition to Six Sigma tools, providing a broader skill set.
Cultural Impact: Six Sigma often requires a change in mindset towards data-driven decision-making and rigorous analysis. Lean Six Sigma also requires a cultural shift but focuses more on continuous improvement and involving everyone in eliminating waste.
Two Main Methodologies of Six Sigma
DMAIC for improving existing products or services.
DMADV is part of the Design for Six Sigma (DFSS), for creating new processes or products.
DMAIC stands for Define, Measure, Analyze, Improve, and Control, focusing on customer satisfaction in manufacturing or service delivery.
In contrast, DMADV—Define, Measure, Analyze, Design, Validate—is used for entirely new designs or when existing solutions don't meet customer needs.
Both require guidance from trained professionals, often learned through certified online programs.
Five Phases of the Six Sigma DMAIC Process
DMAIC is an integral part of Six Sigma's project methodology. It's a data-driven quality strategy used to improve processes. It stands for Define, Measure, Analyze, Improve, and Control.
Here's a breakdown of each phase:
Define: Identify the problem or project goals.
Measure: Quantify the problem.
Analyze: Identify the cause of the problem.
Improve: Implement and verify the solution.
Control: Maintain the solution and ensure improvement.
1. Define
This is the starting point where you clearly state the problem, objectives, and project scope. You identify the requirements of your customers and the goals of the project.
It's crucial to have a clear understanding of what you're aiming to improve and why it's important. You might create a project charter, a document outlining the problem, goal, timeline, team, and other critical project details.
2. Measure
In this phase, you gather data and establish the baseline performance of the process you want to improve. It involves measuring the current system to collect relevant data, which helps in understanding the extent of the problem.
This might include mapping out the process, identifying key performance indicators (KPIs), and using statistical tools to collect and analyze data.
The goal is to have a quantifiable understanding of the process's current state.
3. Analyze
Now, you delve deep into the data collected to identify the root causes of the problem. You'll use various analytical and statistical tools to figure out what's causing the issues.
This might involve techniques like cause-and-effect analysis, hypothesis testing, and regression analysis.
The aim is to pinpoint exactly where and why the process is not performing as desired.
4. Improve
Once the root causes are identified, you develop and implement solutions to address them.
This involves brainstorming potential improvements, selecting the best solutions, and then making changes to the process. It's all about making the necessary adjustments to improve the process's performance.
You might use techniques like the design of experiments to test the changes and ensure they're effective.
5. Control
The final phase is about sustaining the improvements. You put in place controls to ensure that the gains are maintained over time. This might involve updating documentation, implementing training for team members, and setting up ongoing monitoring systems to keep an eye on the process.
The goal is to ensure that the process continues to perform at an improved level and that any deviations are corrected before they become significant issues.
Throughout the DMAIC process, Six Sigma professionals often use a variety of tools such as Pareto charts, fishbone diagrams, control charts, and process mapping.
Each phase builds upon the previous one, ensuring a structured and disciplined approach to quality improvement that's focused on making data-driven decisions and achieving measurable results.
This structured approach is central to Six Sigma methodologies, aiming to improve business processes, meet client expectations, and ensure the quality of existing processes.
Sigma tools are integral to this method, providing the means to analyze and enhance processes systematically. In essence, Six Sigma focuses on a rigorous, data-informed method to uplift and refine business operations, ensuring they align with customer needs and organizational goals.
Five Phases of the Six Sigma DMADV Process
DMADV is primarily used for creating new product designs or process flows where existing systems fail to meet customer needs or when a new market opportunity arises. The goal is to ensure that the design meets client expectations and business requirements from the very beginning.
The acronym DMADV stands for:
Define
Measure
Analyze
Design
Verify/Validate
1. Define
Clearly define the project goals, scope, and customer needs (internal or external). This phase involves understanding the problem or requirement in detail and setting clear objectives.
2. Measure
Measure and identify customer needs and specifications.
This involves collecting data on various factors that affect the process or product, understanding customer expectations, and setting benchmarks.
3. Analyze
Analyze the measured data to determine the best approach or design.
This phase focuses on exploring various options, understanding their impacts, and deciding on the most effective design based on the analysis.
4. Design
Develop and detail the process or product design.
In this phase, the theoretical best design identified in the Analyze phase is turned into a detailed, actionable plan. Prototyping and simulation are often used here to model the outcomes.
5. Verify/Validate
Verify the design performance against customer requirements and validate the design. This final phase involves testing the new design in real-world scenarios to ensure it meets the necessary standards and truly satisfies customer needs before a full-scale launch.
Professionals like Six Sigma Green Belts and Black Belts, often under the supervision of Master Black Belts, typically execute DMADV. They ensure that each step is thoroughly researched, executed, and reviewed for maximum efficiency and effectiveness.
Now that you've understood how the Six Sigma process works, let's take a look at how it plays a significant role in project management.
Project Management Using Six Sigma Tools and Methods
Project management is a critical part of making sure your tasks and goals are on track.
It's about planning, executing, and overseeing a project to ensure it's completed on time and within budget. Whether you're working on a small task or a large-scale project, understanding the basics of project management is essential.
In project management, the sigma process plays a significant role. It's a quality management tool that helps teams reduce errors and improve processes.
By focusing on the Sigma process, teams can achieve higher-quality results and make sure every part of the project meets the necessary quality standards.
A Six Sigma program takes the Sigma process further by providing a structured approach to problem-solving. This program helps teams identify areas where they can improve and provides methods to make those improvements. By participating in a Six Sigma program, you can help your team work more efficiently and produce better-quality results.
One of the goals of using the Sigma process and Six Sigma program is to achieve zero defects. This means that the project or product is free from errors and meets the highest quality standards.
While it's challenging to achieve, striving for it helps teams focus on quality and improvement.
Now, let's talk about how these can make a big difference in nonprofits, organizations focused on helping others rather than making a profit.
Enhancing Nonprofit Efficiency - A Six Sigma Project Example
Six Sigma projects can be a powerful tool for nonprofits. They help ensure that resources are used effectively and that the organization can do as much good as possible.
A sigma project in a nonprofit might look slightly different than in a business. The goal here is not just to save money but to make sure the organization can do as much good as possible.
For example, a nonprofit might use a Sigma project to make sure more of the money donated goes directly to helping people rather than administrative costs.
In these projects, Six Sigma practitioners are the guides. They know the ins and outs of the Six Sigma method and can help the nonprofit figure out where things can be better. They look at the process, find where things are getting stuck or wasted, and suggest improvements.
This isn't just about money; it's about time, effort, and resources too. In a nonprofit, this could mean making sure volunteers are used effectively or that the help they provide really makes a difference.
It's not just for nonprofits, however. Six Sigma can greatly improve efficiency and effectiveness in all kinds of organizations. But who makes these improvements happen?
The "Belts."
Who Makes It Happen? The Belts of Six Sigma
The Belts of Six Sigma are the ones who drive change.
From the Sigma master black belt to those just starting with their Six Sigma certification, each plays a crucial role in total quality management.
They're the problem-solvers and the improvers, the ones who use their skills to make organizations more efficient and effective.
It's all about the people with Six Sigma certification, mostly referred to as "Belts."
Each Belt level has a unique role in driving process improvement and bringing positive change.
They identify problems, find solutions, and help implement changes to improve quality. Whether it's making a process faster, cutting down on waste, or improving a product, they're focused on making things better.

Training and Six Sigma Certifications for Belts
If you are interested in hiring Six Sigma practitioners, here is what you need to know:
Six Sigma Training
Six Sigma training is where practitioners learn all the essentials.
It's designed to teach the techniques and tools needed to improve processes and quality. This isn't just about listening to lectures; it's interactive and practical. Practitioners work on real problems, finding solutions to make a genuine difference.
As they move from one belt level to another, the training gets more advanced, preparing them for greater responsibilities.
During their training, they'll learn how to apply this method to various situations, ensuring they're equipped to tackle challenges effectively.
From defining the problem to analyzing data, improving the process, and then controlling it to make sure the improvements last, training will cover it all.
This ensures they know how to manage each phase effectively.
After completing their training, they'll have the opportunity to earn Six Sigma certification.
Six Sigma Certifications
The Six Sigma certification proves that practitioners have the skills and knowledge needed to contribute to quality improvement projects. It's a recognition of their dedication and expertise, and it can be a significant boost to their career.
Whether they're just starting with the basics or aiming for a higher-level belt or Six Sigma black belt, this training can provide them with the skills and knowledge they need.
Six Sigma Green Belts
Individuals who earn the title "Green Belts" play a vital role. These professionals have completed specific Sigma Green Belt training, equipping them with the tools and knowledge to guide and support projects within their organization.
Green Belts are team members who work on process improvement projects part-time, alongside their regular work duties. They understand Six Sigma techniques and can apply them to enhance business processes. Their training involves a mix of classroom learning and hands-on project work, ensuring they can put their new skills into action right away.
With their training, Green Belts help to solve quality issues and improve processes, making sure everything runs smoothly and efficiently. They often work under the guidance of more experienced Six Sigma professionals, like Black Belts or Master Black Belts, who mentor and support them through complex projects.
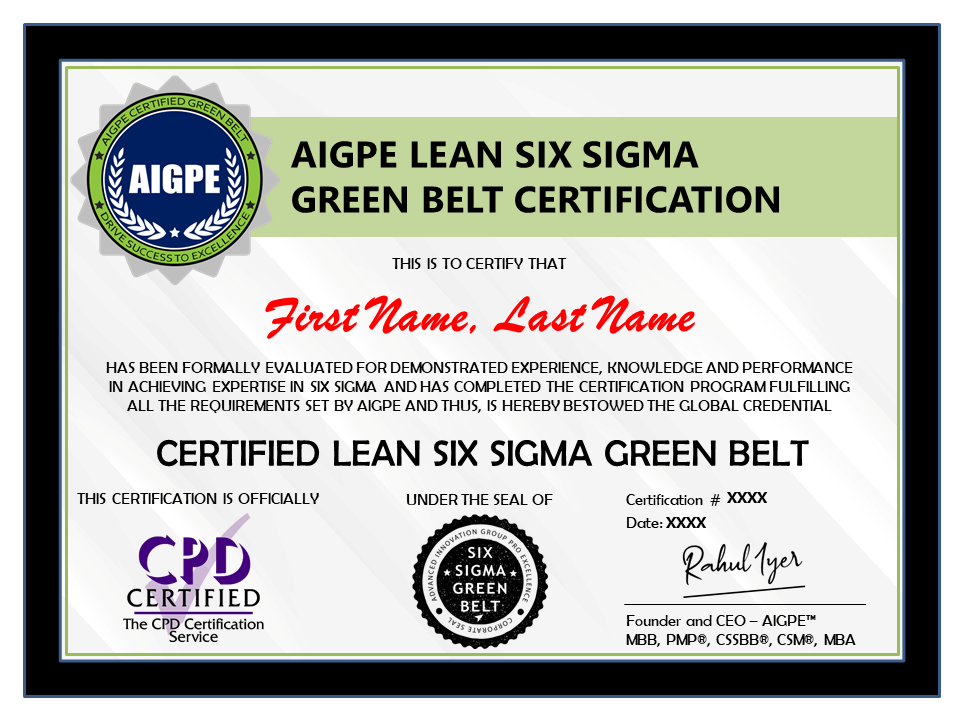
So, if practitioners are interested in making a real difference in their organization, Sigma Green Belt training might be the perfect next step for them.
Six Sigma Black Belts
Six Sigma Black Belts are key players in the quest for quality and efficiency in businesses. They stand out for their deep understanding and expert-level training in the Six Sigma methodology. Black Belts have dedicated significant time and effort to master the techniques that drive substantial improvements in business processes.
These professionals don't just learn; they lead. Black Belts are well-equipped to head up projects and guide teams toward success. They are the problem-solvers and change-makers, often working full-time on Six Sigma initiatives. Their role involves analyzing complex problems, making data-driven decisions, and finding innovative solutions that make a real difference.
Their training is rigorous, covering a broad range of strategies and tools to understand and improve every aspect of a process. This intense focus ensures that when a Black Belt works on a project, they're not just aiming for incremental changes; they're reshaping entire processes to make them leaner, more efficient, and more effective.
Certified Master Black Belt (CMBB)
The Certified Master Black Belt (CMBB) is a prestigious title in the world of Six Sigma. It represents a deep understanding and mastery of Six Sigma principles and practices.
A CMBB is an expert in sigma quality. This means they don't just understand the Six Sigma process; they know how to apply it in various situations to improve quality and efficiency. They are the ones who oversee projects and ensure that everything runs smoothly and effectively.
One of the critical roles of a CMBB is to mentor and guide sigma green belts and six sigma black belts. They share their knowledge and experience, helping others grow in their Six Sigma journey. Their guidance is crucial in helping teams solve complex problems and achieve significant improvements.
Conclusion
In wrapping up, remember that diving into Six Sigma isn't just about tackling process variation; it's about embracing a business strategy dedicated to sustained quality improvement.
This approach not only shines a light on where things might be going off track, but it also guides you in refining every step along the way. Imagine Six Sigma as a trusted mentor for your team, always there to ensure operational excellence remains at the heart of all you do.
Think of quality control not as a one-time fix but as a continuous journey toward excellence.
Whether you're starting fresh or seeking to enhance what's already there, the Six Sigma method stands as a beacon, guiding your path to better, more reliable processes.
So, as you step forward, carry with you the lessons and strategies of Six Sigma, and watch how Six Sigma implementation can transform your approach to quality and efficiency.
Comments