STRATEGIC PLANNING | BUDGET thoughts starters ... (part 2)
- Richard Kunst
- Nov 7, 2021
- 5 min read
As fall approaches many organizations begin the planning process for the coming year. Typically part of the planning process involves implementing some Process Improvements so we decided to share some methodologies and the typical benefits that can be achieved ...
HOURLY RUN BOARDS
This is a great pre-cursor to implementing an Overall Equipment Effectiveness metric. It establishes hourly expectations providing immediate feed-back to employees and makes visible quickly any disturbances to flow ... if you have a realistic target it is a natural human tendency to attempt to achieve it.
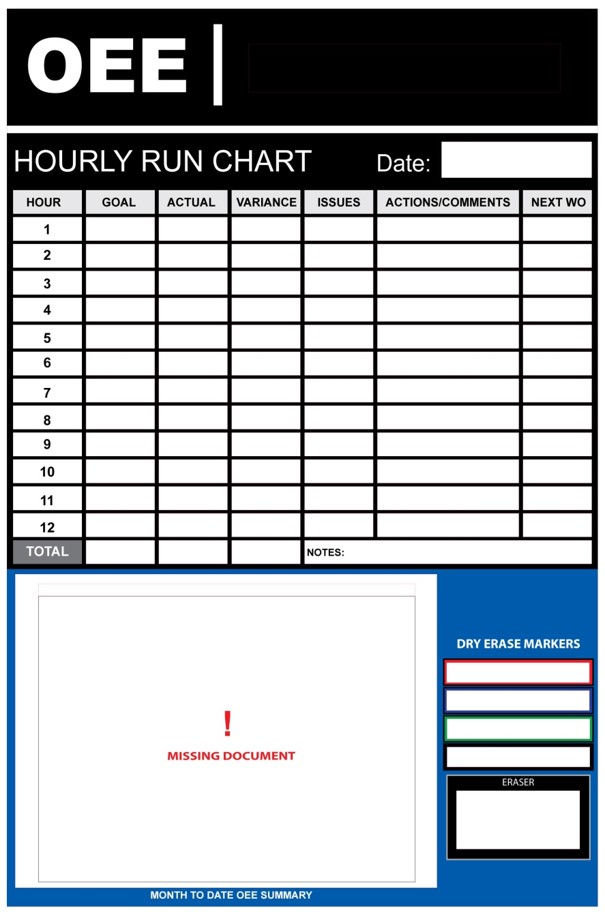

VISUAL ATTENDANCE
Do you know what your casual absenteeism rate is as a percentage? This is the silent cancer of productivity in your operation. Determine your rate and then calculate it as a percentage of your payroll costs ... what would cutting it half provide in savings?
Making it visual creates peer pressure for correction, it also reinforces our good performers that management is looking at attendance in a very real way. I have created an Adult to Adult environment and as an adult you have responsibilities including being at work on time. As attendance improves the start of shift labour shuffle diminishes increasing start of shift production.
Our minimum expectation is a 50% improvement within 3 months of commencement which typically will increase your productivity by 10% plus the payroll savings.
KEY PERFORMANCE INDICATORS (KPI)
We know you want to increase profitability by 10-20%, improve quality by an X factor ... but how are your employees supposed to contribute? The higher in the organization you are the more number driven you become ... meanwhile the front-line employees are still task or widget driven. Insure that your identified KPI's are controllable by the team members ... so instead of asking for a
10% productivity improvement convert that into a unit improvement.
For example a study revealed that if a Doctor were to see 1
additional patient per day it could increase their annual income by o
ver 60K.
CELLS | SINGLE PIECE FLOW
Give me a process and I will convert it into a cellular operation typically improving through-put by 50-100%. Can you tell that i really like creating Cells ... there are different approaches for creating a cellular layout with either having the person moving from task to task with the material or having the material flow from task to task in a single piece flow methodology.
In a manufacturing operation we were able to eliminate batch processing by adopting single piece flow and cellular manufacturing to reduce inventory by 80%, reduce our labour from 60 people per shift to 16 while improving our safety record ... not to mention all of the floor space harvested for additional business.
Cells work great in operations but also really work tremendous in office and administration environments to improve velocity (remember how we discussed cadence earlier). Typically we see an order being processed in the back office consuming close to 80% of the quoted Process Lead Time and this activity is typically non-value add.
Implementing Cells can be challenging but the rewards remarkable. At La-Z-Boy our adoption of cellular manufacturing allowed us to reduce our Process Lead Time from 14-16 weeks to 4 hours consistently and now our plant managers are bored since they are no longer fire fighting but focused on CI.
Plus with velocity comes improved margin and the ability to seize opportunities away from competitors ... a strong argument for on-shoring.
WORKPLACE ORGANIZATION | 5S+1
You have the product or service and the technology for delivery ... but it is the execution of your professionals that actually make it happen. No matter what the role each individual is a professional that deserves to work in a professional environment and this is your responsibility!
Typically this is the first Lean Methodology organizations embrace since it has such a huge visual impact. However in many cases it just becomes a housekeeping initiative. At times 5S can be difficult to quantify because we poorly document lost time due to searching, wasted walk patterns repetitive reaching etc.
Set your standards high to create that "WOW" plant that everyone will be proud to be part of. I know that it easy to slap some paint on a piece of plywood to create a shadow board for tools ... but is that the professional image you want to project? When I look at our 5S applications we provide today compared to several years ago we truly have set a new standard of professionalism.
A well organized plant sells itself from the aspect of recruiting and retaining great employees to selling to your customers. In a former life I can count contracts awarded in the millions of dollars because our plant was clean and well organized which communicated that we had little waste, high quality along with strong efficiencies typically the contract was signed before the plant tour ended.
LEAN LEADER TRAINING
People don't know what they don't know. Make sure you complement the implementation of initiatives with training to increase the intellectual quotient of your organization. Over the years we have assembled our training tool box of experiential learning methodologies into a curriculum. As we take our folks through the training ... they learn in a safe environment in a hands-on manner then need to apply the learning's through homework assignments. We then audit the homework as a test for understanding by the attendees before moving to the next subjects.
As we expand and increase the comprehension of our employees and expand the area of empowerment both the employees and the organization wins big time. In one example we trained a bunch of employees with just an expectation of increasing their awareness ... just imagine how happy the organization was when after applying some of the methodologies they were able to increase through-put by 300%.
CONCLUSION
You may be already using some of the suggested methodologies or you may need to drill deeper inside of them to optimize the potential. Of course there are many additional powerful methodologies that deliver amazing results ... but these suggested can be applied in almost any type of operation. In summary here is the potential impact;
Daily Report-Outs -- 20 - 30% productivity Improvement
Visual Attendance -- 2-4% of annual payroll savings
Hourly Run Boards -- 20% Productivity Improvement
TPM -- 20 -30% unscheduled downtime reduction + 10% productivity improvement
Cells -- 50 to 100% through-put improvement
Lean Leader Training -- 20% Improvements minimum in Quality, Problem Solving and Through-put
Save Implementation Time by accessing us for custom tailored solutions specific to your operation.
: Supporting Products and Templates are available through the Kunst Solutions Store.
: Coaching and Facilitation is available through Kunst Solutions Corp.
We are practitioners wanting to help other practitioners !!!
Comments