Top Lean Manufacturing Consultant: Kunst Solutions
- Richard Kunst
- Oct 11, 2023
- 6 min read
In order to improve your business operations, you may be looking for Lean manufacturing consultants. Lean is, after all, an excellent methodology to improve your processes. But without the right experts, your company can lose a lot of time and money.
That’s where Lean manufacturing consultants come in.
Kunst Solutions is a top lean manufacturing consultant based out of Toronto, Canada, but it operates internationally with clients in Canada, Europe, and the United States. Over the past 15 years, we have worked with 213 companies and counting, saving them a total of over $100M.
Lean Manufacturing Consulting | Lean Consulting Firms
Lean manufacturing consultants provide businesses with a systematic approach to optimizing operations. Rooted in the principles of lean manufacturing, this consulting approach emphasizes the elimination of unnecessary waste from manufacturing processes while ensuring a consistent focus on customer value.

Engaging with reputable lean consulting firms like Kunst Solutions ensures that businesses access a wealth of knowledge on methodologies such as the Toyota Production System and Lean Six Sigma. These methodologies not only streamline production processes but also drive continuous improvement throughout an organization's supply chain.
By partnering with adept manufacturing consultants, companies can delve deeper into the facets of supply chain management and lean process adaptations and harness strategies that spotlight customer satisfaction while balancing cost-effective operations.
Transforming Your Manufacturing Processes with Lean
At its core, lean manufacturing is about understanding and delivering customer value. It's an approach that relentlessly seeks to minimize waste — whether in terms of time, materials, or resources — while maximizing productivity. The principle is simple, yet its execution can be transformative.

When you delve into lean principles, you find that they target the very essence of manufacturing processes. By identifying and eliminating unnecessary waste, businesses can dramatically reduce lead times, improve product quality, and enhance overall customer satisfaction.
Key methodologies within Lean, such as the Toyota Production System, provide a framework for this transformation. It emphasizes the importance of continuous flow and pull-based systems, ensuring that products are manufactured precisely when they're needed, reducing inventory costs and waste.
Benefits of Lean Manufacturing
Lean manufacturing, rooted in principles of efficiency and value delivery, offers a multitude of advantages to businesses eager to optimize their operations.
Here's a breakdown of the key benefits:
Waste Reduction
Lean principles target the elimination of inefficiencies and redundancies and ensure resources are utilized to their fullest potential.
Improved Productivity
Streamlined processes and continuous flow methodologies, such as the Toyota Production System, drive higher output with the same or fewer resources.
Enhanced Quality
With a focus on standardized processes and continuous improvement, lean manufacturing aims to reduce defects and improve product consistency.
Cost Savings
By reducing waste, optimizing inventory, and improving process efficiency, businesses can realize significant cost reductions.
Shorter Lead Times
Lean practices, such as Just-In-Time (JIT) production, ensure products are manufactured and delivered more swiftly, leading to faster customer response times.
Increased Customer Satisfaction
By prioritizing customer value and delivering high-quality products promptly, businesses can boost customer loyalty and retention.
Employee Engagement
Lean fosters a culture of collaboration and continuous improvement, leading to increased morale and a more engaged workforce.
Flexibility and Adaptability
Lean organizations can more easily adjust to market changes, ensuring they remain competitive in dynamic environments.
Sustainable Practices
With a focus on reducing waste and optimizing resources, lean manufacturing often aligns with environmentally-friendly practices.
Holistic Supply Chain Optimization
Lean principles, when applied to supply chain management, ensure seamless integration from raw material procurement to final product delivery.
By comprehending and harnessing these benefits, businesses can steer towards operational excellence, ensuring resilience, profitability, and a customer-centric approach in a rapidly changing marketplace.
What is a Lean Six Sigma Consultant?
For many, the terms 'Lean' and 'Six Sigma' might appear synonymous or interchangeable, which leads to some confusion. This is especially true for those seeking a Lean Manufacturing Consultant but stumbling upon the term Lean Six Sigma Consultant.
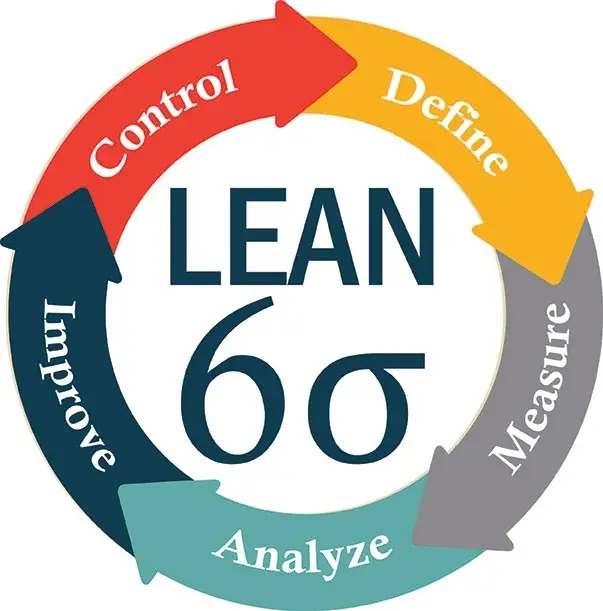
Let's demystify this:
Lean vs. Lean Six Sigma
While 'Lean' primarily focuses on eliminating waste and streamlining processes, 'Six Sigma' zeroes in on reducing process variability and improving quality through data-driven decisions.
When combined, Lean Six Sigma encapsulates the strengths of both methodologies, offering a holistic approach to process improvement and efficiency.
A Lean Six Sigma Consultant specializes in this combined methodology.
They are adept at:
Identifying and Eliminating Waste: Drawing from the principles of Lean, they pinpoint areas of inefficiency – be it in terms of time, motion, inventory, or other resources.
Data Analysis and Quality Improvement: Borrowing from Six Sigma's toolkit, these consultants utilize statistical methods to understand process variations, aiming to enhance product or service quality.
Strategic Integration: They ensure that the combined principles of Lean and Six Sigma are seamlessly integrated into the organization's operations, fostering a culture of continuous improvement.
Why the Overlap?
Given that Lean Six Sigma amalgamates the core principles of both methodologies, it's understandable that those seeking guidance in Lean Manufacturing might inadvertently search for a Lean Six Sigma consultant.
This convergence reflects the evolving nature of operational excellence methodologies and the desire for a comprehensive approach to process improvement.
In essence, a Lean Six Sigma Consultant offers the best of both worlds. They harness the waste-reducing principles of Lean while integrating the precision and data-centric quality improvement techniques of Six Sigma.
For organizations aiming for a holistic transformation, understanding the role and expertise of such a consultant can be invaluable.
Using Lean Six Sigma
Lean Six Sigma merges the efficiency-driven principles of Lean with the data-centric focus of Six Sigma.
In recent years, it has risen to prominence as a powerful tool for organizational improvement. However, to unlock its full potential, businesses often require a depth of understanding that only expert guidance can provide.
Here are a few reasons why Lean Six Sigma requires expert guidance from Lean manufacturing consultants:
Complexity of Implementation
While the principles of Lean Six Sigma might appear straightforward, their implementation across varied business processes can be intricate. Missteps or oversights can dilute the effectiveness of the methodology.
Data-Driven Decisions
One of the core tenets of Six Sigma is the emphasis on data. An expert can help organizations gather, analyze, and interpret data correctly, ensuring decisions are backed by tangible evidence and not just intuition.
Tailored Solutions
Lean Six Sigma isn't a one-size-fits-all solution. Each organization has unique challenges. An expert can customize the application of the methodology, ensuring it aligns with the specific needs and objectives of the business.
Training and Development
Deploying Lean Six Sigma requires a trained workforce. An experienced guide can provide comprehensive training, ensuring that team members are well-equipped to leverage the methodology's tools and techniques.
Continuous Improvement
Lean Six Sigma is not a static process; it demands regular reviews and iterations. An expert ensures that businesses maintain this momentum, always striving for higher levels of excellence.
Avoiding Common Pitfalls
With their vast experience, experts can foresee potential challenges or common errors that businesses might encounter. Their guidance can help organizations navigate these pitfalls with ease.
Stakeholder Buy-In
For Lean Six Sigma to be effective, it's essential that all stakeholders, from top management to frontline workers, are on board. Experts can articulate the benefits and processes in a way that secures this crucial buy-in.
Measurable Outcomes
With an expert's touch, businesses can set clear, measurable objectives for their Lean Six Sigma initiatives, ensuring accountability and tangible results.
Why Hire Kunst Solutions as your Lean Manufacturing Consultants
Kunst Solutions offers a comprehensive consultancy service grounded in a deep understanding of lean methodologies. Over the past 15 years, we’ve worked with 213 companies and counting, saving them over $100M in total.
Here are the main reasons to consider Kunst Solutions for lean manufacturing consultancy:
Established Track Record: Kunst Solutions has consistently demonstrated proficiency in lean manufacturing, effectively transforming diverse manufacturing processes into more efficient systems.
Customized Solutions: Every organization presents unique challenges. Kunst Solutions emphasizes crafting strategies specific to individual organizational needs, ensuring an integrated lean approach across all operations.
Emphasis on Data: Incorporating elements from Six Sigma, Kunst Solutions relies on a data-driven approach, ensuring decisions and strategies stem from solid analytical findings.
Continuous Improvement Ethos: Kunst Solutions promotes the principle of continuous improvement, aiding organizations in adapting and evolving in the dynamic manufacturing sector.
Focus on Employee Participation: Recognizing that lean principles are most effective when all team members are involved, Kunst Solutions offers training and resources to ensure active employee engagement in the lean transformation process.
Global Perspective, Local Implementation: While drawing from international best practices, Kunst Solutions appreciates the nuances of local contexts. Their consultancy ensures that global insights resonate with the specific cultural and operational landscape of each organization.
Clear Communication: Kunst Solutions prioritizes open dialogue with all stakeholders, ensuring clarity in setting objectives, updating progress, and addressing any challenges.
Result-Oriented Approach: Beyond the implementation of strategies, Kunst Solutions is committed to achieving measurable outcomes, ensuring that the adoption of lean methodologies translates to tangible improvements.
Kunst Solutions presents a blend of experience, methodical approach, and dedication, making it a considerable choice for organizations aiming to embed lean principles in their manufacturing processes. To learn more about Kunst Solution’s consulting services, book a complimentary call today.
Comments