What is the Toyota Production System?
- Richard Kunst
- Dec 4, 2023
- 9 min read
In manufacturing and continuous improvement, the Toyota Production System (TPS) holds a distinguished place. Developed by Toyota, one of the world's leading automobile manufacturers, TPS has become a model for efficient production practices.
In this blog post, we will delve into the fundamental principles and methodologies that define TPS. Our goal is to provide a clear understanding of how this system has left an indelible mark on the manufacturing world and what you can learn from it.
The Genesis of the Toyota Production System (TPS)
The story of the Toyota Production System (TPS) traces its roots back to the aftermath of World War II in Japan.

At that time, the landscape was marred by economic devastation, and resources were scarce. It was under these challenging conditions that Toyota, a fledgling automobile manufacturer, set out to redefine the very principles of production.
At the heart of this transformation was Taiichi Ohno, an engineer at Toyota who played a pivotal role in developing the system. Ohno's mission was clear: to find a way to compete with well-established American automobile manufacturers in a resource-constrained environment.
Ohno and his team embarked on a journey of continuous improvement, seeking to eliminate waste, optimize production processes, and maximize efficiency. They drew inspiration from various sources, including American supermarkets and the work of quality pioneers like W. Edwards Deming.
Over time, these influences coalesced into a uniquely Japanese approach to manufacturing excellence—the Toyota Production System.
Why the Toyota Production System was Invented
The creation of TPS was born out of necessity and a relentless pursuit of innovation.
Toyota's survival in the post-war era depended on its ability to produce high-quality vehicles efficiently. With limited resources and a desire to avoid overburdening the workforce, TPS emerged as a solution addressing economic and human concerns.
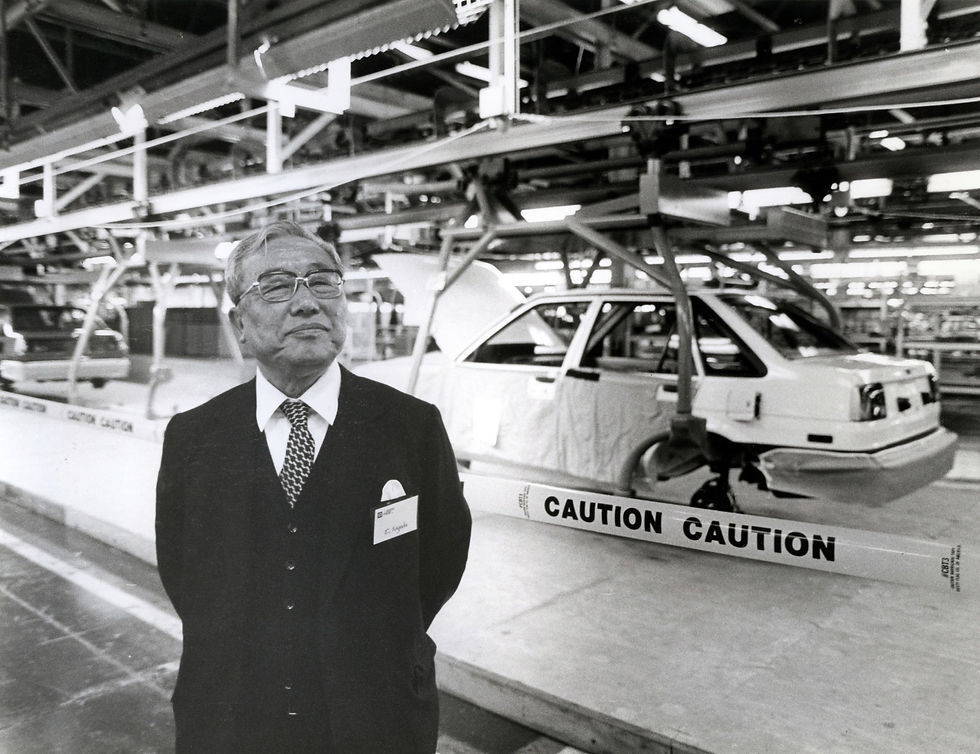
The underlying philosophy of TPS, emphasizing eliminating waste, optimizing processes, and valuing the human element in production, was a response to the challenges of the time. It wasn't simply a means to survive; it was a vision for thriving in an ever-changing global marketplace.
The Toyota Production System (TPS) wasn't a sudden invention but a gradual evolution driven by necessity and innovation. It emerged in post-war Japan as a response to economic challenges and the need for a competitive edge in manufacturing, and today it remains one of the most respected continuous improvement methods.
Understanding the Toyota Production System: The Cornerstones
The Toyota Production System (TPS) is a holistic approach to achieving manufacturing excellence. At its core, TPS seeks to eliminate waste, streamline processes, and maximize efficiency.

This methodology has garnered worldwide recognition for its impact on the production industry.
Within the TPS framework, two cornerstone components stand out: Lean Manufacturing and Six Sigma.
These components serve as the foundation upon which TPS builds its success:
Lean Manufacturing
Lean Manufacturing, a concept deeply integrated into TPS, emphasizes the elimination of waste in all its forms. From excess inventory to inefficient processes, Lean Manufacturing meticulously identifies and eradicates these inefficiencies, ensuring that each aspect of production adds value.
The result? A leaner, more efficient production process that optimizes resources and minimizes unnecessary costs.
Unveiling Lean Principles
Lean manufacturing principles lie at the heart of the Toyota Production System (TPS). These principles guide organizations toward efficient production and continuous improvement.
Just-in-Time (JIT) Production
One of the core principles of Lean Manufacturing is JIT production. It involves producing only what is needed, when it is needed, and in the exact quantity required. JIT minimizes excess inventory, reduces storage costs, and enhances overall production efficiency.
Continuous Improvement
The pursuit of continuous improvement is synonymous with Lean Manufacturing. This principle encourages organizations to regularly review processes, identify inefficiencies, and implement enhancements. It fosters a culture of innovation and incremental progress.
Eliminating Waste
Lean Manufacturing is all about waste reduction. This includes eliminating various forms of waste, such as overproduction, waiting time, unnecessary transportation, excess inventory, and defects. By eliminating waste, organizations optimize resources and improve efficiency.
Six Sigma
Six Sigma, another vital component within TPS, focuses on pursuing perfection and quality control. It provides a structured approach to problem-solving and process improvement, aiming to reduce defects and variations in production.
By adhering to the Six Sigma methodology, TPS ensures that every product meets rigorous quality standards, enhancing customer satisfaction and trust.
Defining Six Sigma
At its core, Six Sigma is a data-driven methodology that aims to minimize defects and variations in processes. It seeks to achieve near-perfect quality and consistency by reducing the likelihood of errors to a statistically improbable level – six standard deviations away from the mean, hence the name "Six Sigma."
DMAIC Methodology
Six Sigma follows the DMAIC (Define, Measure, Analyze, Improve, Control) methodology. This structured approach provides a framework for organizations to identify and rectify process deficiencies systematically.
Data-Driven Decision Making
A distinguishing feature of Six Sigma is its reliance on data and statistical analysis. This ensures improvements are based on concrete evidence rather than intuition or guesswork.
At its core, TPS is a comprehensive system that integrates Lean Manufacturing and Six Sigma principles to achieve manufacturing excellence. Its commitment to eliminating waste and maintaining the highest quality standards has made it a benchmark for efficiency and productivity in the manufacturing industry.
The Human Element in the Toyota Production System
The Toyota Production System (TPS) places a significant emphasis on the human element in achieving its remarkable success. It recognizes that people are not just cogs in a machine but are pivotal contributors to the system's effectiveness.
In the world of TPS, the philosophy extends far beyond the assembly line. It transforms the way people work and collaborates within organizations. Employees become active participants in identifying inefficiencies, suggesting improvements, and ensuring a smooth production flow.
This philosophy encourages a culture of continuous learning and adaptation, where individuals and teams are empowered to take ownership of their roles. As a result, TPS not only enhances operational efficiency but also fosters a sense of purpose and pride among those who play a role in its implementation.
TPS in Global Business
The influence of the Toyota Production System (TPS) transcends geographical borders and penetrates various industries worldwide. Its principles and practices are embraced across continents, revolutionizing how organizations approach manufacturing and continuous improvement.

From automotive manufacturing to electronics, healthcare, and beyond, TPS principles have found a home in diverse industries. Companies across the globe have recognized the value of TPS in reducing waste, improving quality, and increasing efficiency.
Notable success stories abound, with organizations achieving remarkable transformations through adopting TPS. Case studies highlight how TPS principles have enabled businesses to streamline processes, reduce costs, and deliver products and services that meet the highest standards of quality.
Here are some examples:
Automotive Manufacturing: Ford Motor Company
The Ford Motor Company embraced TPS principles to enhance its manufacturing processes.
By implementing Lean Manufacturing techniques inspired by TPS, Ford reduced production cycle times and achieved significant cost savings. This transformation revitalized the company's competitiveness and allowed it to adapt swiftly to changing market demands.
Electronics: Apple Inc.
Apple Inc., the iconic tech giant, incorporated TPS-inspired practices into its supply chain management.
By minimizing inventory and optimizing production flow, Apple delivers its coveted products to consumers worldwide efficiently. This approach has not only reduced waste but also played a pivotal role in maintaining Apple's reputation for high-quality, innovative products.
Healthcare: Virginia Mason Medical Center
The Virginia Mason Medical Center in Seattle, Washington, is a shining example of TPS application. Facing the challenge of improving patient care while controlling costs, they turned to TPS for solutions. By implementing Lean principles borrowed from TPS, Virginia Mason achieved remarkable results, reducing wait times, enhancing patient safety, and improving overall operational efficiency.
Retail: Walmart
The world's largest retailer, Walmart, has applied TPS concepts to its supply chain and inventory management processes.
By adopting just-in-time inventory practices and optimizing logistics, Walmart has kept prices low for customers while maintaining a vast and diverse product selection. This strategic application of TPS principles has played a crucial role in Walmart's success in the competitive retail industry.
The Learning Journey in TPS
Learning is a perpetual journey in the Toyota Production System (TPS). It's not just about mastering processes; it's about developing a continuous improvement mindset.
Learning and Adaptation
Individuals and teams within organizations that adopt TPS principles embark on a journey of learning and adaptation. They learn to identify inefficiencies, eliminate waste, and optimize processes. But it goes beyond technical skills; TPS fosters a culture of problem-solving and innovation.
Continuous Learning and Knowledge Sharing
One of the distinguishing features of TPS is its emphasis on continuous learning and knowledge sharing.
Within TPS, employees are encouraged to share insights, challenges, and solutions with one another. This collaborative approach leads to a wealth of collective knowledge that drives ongoing improvement.
TPS recognizes that learning is not confined to a specific phase but is an integral part of daily operations. It's a journey where individuals and teams evolve, adapt, and innovate together.
Toyota's Vision of the Ideal
At the core of the Toyota Production System (TPS) lies a vision of the "ideal state." This vision is a guiding light, propelling TPS towards perfection and efficiency.
The Concept of the "Ideal State"
The "ideal state" in manufacturing and operations, as envisioned by Toyota, is a state of perfection—a state where everything operates flawlessly, waste is eliminated, and processes are optimized.
It's a state where every product is of the highest quality, every step in the production process adds value and every resource is used efficiently.
Continuous Perfection: TPS strives for perfection in production processes. While perfection may be elusive, this relentless pursuit ensures that organizations continuously improve and optimize their operations.
Customer-Centric Approach: TPS centers on meeting customer demands efficiently and with the highest quality. By aligning production with customer needs, organizations enhance customer satisfaction and loyalty.
Striving for Perfection and Efficiency
TPS tirelessly strives to achieve this ideal state.
It acknowledges that perfection may be unattainable, but the relentless pursuit of perfection leads to continuous improvement and unparalleled efficiency. By setting the bar high, TPS ensures that every effort is made to minimize waste, enhance quality, and optimize operations.
In summary, the "ideal state" in TPS is a guiding principle that inspires continuous improvement and drives the quest for perfection and efficiency in manufacturing and operations.
Learning from the Toyota Production System (TPS): Strategies for Businesses
In our exploration of the Toyota Production System (TPS), we've unveiled the core principles and philosophies that have made it an unparalleled model for manufacturing and continuous improvement.
This section delves deeper into the essence of TPS, revealing how its commitment to efficiency, trust, and excellence transcends processes.
Efficiency Through Automation
Automation is a fundamental component of TPS. The system recognizes the value of automating repetitive and labor-intensive tasks, liberating human resources for more complex and value-added activities.
By embracing automation, businesses reduce lead times, improve product consistency, and enhance efficiency.
Building Mutual Trust with Suppliers and Customers
In the TPS framework, the relationships between suppliers, manufacturers, and customers are pivotal.
Trust is cultivated through transparent communication and fair dealings.
Suppliers are viewed as strategic partners, integral to the production process.
This mutual trust results in reliable supply chains and high-quality products.
The Scientific Method Applied
TPS is inherently rooted in the scientific method. It encourages organizations to form hypotheses, conduct experiments, gather data, and make informed decisions based on evidence.
This rigorous approach ensures that improvements are not based on guesswork but on sound analysis and empirical observations.
Reducing Waste Systematically
The reduction of waste is a central tenet of TPS. By systematically identifying and eliminating waste in all forms, from excess inventory to defects, businesses can optimize their operations.
TPS encourages organizations to focus on value-added activities and to eliminate anything that does not contribute to the final product.
Standardized Work for Consistency
Standardization is a key aspect of TPS. It involves defining clear and repeatable processes that minimize variations and errors.
Standardized work ensures that employees follow established procedures, reducing the chances of defects and enhancing overall quality.
Stimulating Personal and Professional Growth
TPS places great importance on personal and professional growth. It encourages employees to expand their skills, take on new responsibilities, and contribute to the organization's success.
This focus on individual development fosters a culture of continuous learning and improvement.
Long-Term Vision and Correct Decisions
TPS is not about quick fixes; it's about long-term vision. It compels organizations to make decisions that align with their strategic goals and the "ideal state" they aim to achieve.
By focusing on the big picture and resisting short-term gains, businesses can ensure sustained success.
A Learning Organization
TPS transforms organizations into learning entities. It encourages employees at all levels to seek knowledge, share insights, and engage in problem-solving.
This collaborative approach creates a dynamic learning culture where improvements are an ongoing journey rather than a destination.
Leading by Example
In the world of TPS, leadership plays a pivotal role. Leaders are expected to lead by example, embodying the principles of TPS in their actions and decisions.
They set the tone for the organization's commitment to continuous improvement and excellence.
Meeting Challenges Head-On
Challenges are not viewed as obstacles but as opportunities for improvement within TPS. Businesses are encouraged to embrace challenges, as they often lead to innovations and breakthroughs.
The TPS mindset encourages organizations to confront difficulties with resilience and determination.
Striving for Excellence Every Day
In essence, TPS is a philosophy of excellence that permeates every facet of an organization. It's about doing things better today than yesterday and continuously seeking ways to optimize processes, reduce waste, and enhance quality.
The Toyota Production System (TPS) is a holistic approach to manufacturing and continuous improvement that goes beyond processes and techniques. It's a philosophy of efficiency, trust, and a commitment to excellence.
By embracing the principles of TPS, businesses can not only enhance their operations but also cultivate a culture of growth, learning, and innovation that paves the way for long-term success in an ever-evolving business landscape.
Need Help Implementing Continuous Improvement in Your Business?
Embarking on the path of continuous improvement can be a transformative journey for your business. However, it's not always easy to navigate alone.
If you're eager to embrace the principles of the Toyota Production System (TPS) and incorporate them into your operations but need guidance and expertise, we're here to help.
Book a Consultation with Kunst Solutions
At Kunst Solutions, we specialize in helping businesses like yours unlock their potential through TPS-inspired strategies.
Our consulting services are tailored to your unique needs and objectives, whether you want to streamline processes, reduce waste, or enhance quality.
By booking a consultation with us, you'll have the opportunity to:
Gain a deeper understanding of how TPS principles can benefit your specific industry and operations.
Receive personalized guidance on implementing continuous improvement strategies that align with your business goals.
Explore real-world case studies and success stories that showcase the impact of TPS in various industries.
Take the first step towards a journey of efficiency, excellence, and continuous growth.
Don't miss the chance to transform your business with the power of TPS.
Contact Kunst Solutions today, and let's embark on a journey towards continuous improvement together.
Comments